Introduction
Table of Contents
ToggleIf you manage a fleet of electric forklifts, you’re likely familiar with the routine of battery watering. For decades, it’s been an unavoidable part of operating lead-acid-powered equipment. The regular topping-off with distilled water, the checking of electrolyte levels, and the occasional acid spill are all part of the job. But in 2025, with advancements in battery technology, is this laborious process still necessary?
As a manufacturer of lithium-ion batteries designed specifically for electric forklifts, we at [Your Company Name] often encounter this question. Potential clients, accustomed to the demands of lead-acid batteries, are curious about the alternatives. They want to know if the upfront investment in lithium-ion is genuinely justified and if it eliminates the need for battery watering kits and all the associated tasks.
This guide isn’t a sales pitch disguised as information. We’ll present a balanced, objective comparison of lead-acid battery watering systems and the lithium-ion alternative. We’ll delve into the actual costs – not just the price of a fork truck battery watering system but also the hidden expenses of labor, downtime, and potential battery damage. We aim to provide B2B decision-makers – forklift dealers, brand representatives, warehouse managers, and logistics professionals – with the knowledge they need to make the best choice for their specific operational needs.
Lead-Acid Battery Watering: A Deep Dive into the “Why” and “How”
Before we discuss alternatives, it’s essential to understand why lead-acid forklift batteries require watering. It’s not a design flaw; it’s inherent to the battery’s chemistry.
Unlike sealed lithium-ion batteries, lead-acid batteries have vents. During the charging process, a chemical reaction occurs within the battery cells. This reaction, called electrolysis, breaks down some of the water in the electrolyte solution (a mixture of sulfuric acid and water) into its components: hydrogen and oxygen gas. These gases are then vented out of the battery.
This water loss is unavoidable. If the electrolyte level drops too low, exposing the lead plates inside the battery to air, several detrimental things happen:
Sulfation:
- Lead sulfate crystals begin to form on the exposed plates. These non-conductive crystals effectively reduce the battery’s active surface area and diminish its capacity to store and deliver energy. This is a primary cause of lead-acid battery failure.
Overheating:
The electrolyte solution is crucial in dissipating heat generated during charging and discharging. A battery with less electrolyte is more prone to overheating, which can accelerate sulfation and damage internal components.
Reduced Lifespan:
- Consistent under-watering dramatically shortens the battery’s overall lifespan, leading to more frequent and costly replacements.
Therefore, regular and correct watering is critical for maintaining lead-acid forklift batteries’ health, performance, and longevity. It’s not an optional maintenance task; it’s a fundamental requirement. It must be done with distilled or deionized water; tap water contains minerals that will contaminate the electrolyte and damage the battery.
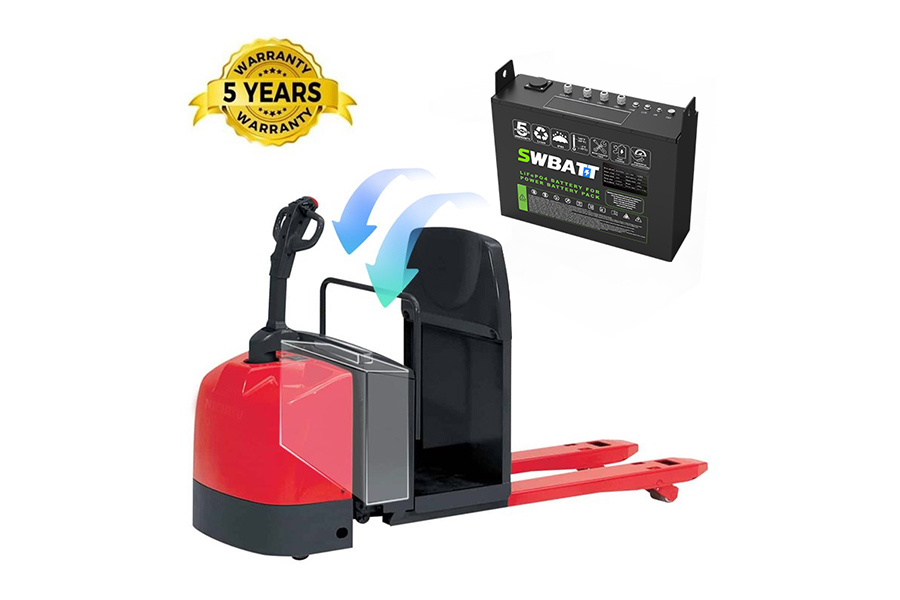
Exploring Fork Truck Battery Watering System Options: From Manual to Automatic
Given the necessity of watering, various systems have been developed to simplify and streamline the process. These range from basic manual methods to sophisticated automated solutions. Here’s a breakdown:
- Manual Battery Watering:
- Description: This is the most basic approach, involving manually pouring distilled water into each battery cell using a container like a watering can, a specialized forklift battery filler bottle, or a gravity-fed tank with a nozzle.
- Pros: The lowest upfront cost. The equipment is simple and readily available.
- Cons: The most time-consuming and labor-intensive method. It’s highly prone to human error – overfilling and underfilling are common. Overfilling can cause acid spills, creating safety hazards and corroding the battery and surrounding equipment. Underfilling leads to the problems described above (sulfation, overheating). It also increases the risk of direct contact with battery acid, requiring careful use of personal protective equipment (PPE). (Image: A simple hand-held battery filler bottle. Image text: “Manual Battery Filling: Labor-Intensive and Prone to Errors”)
- Single-Point Watering Systems (SPWS):
- Description: These systems, often sold as forklift watering system kits, consist of a network of interconnected tubes and valves permanently installed on the battery. Each cell has a float valve that automatically shuts off the water flow when the correct electrolyte level is reached. A single fill point connects to a water source (typically a deionizer or a container of distilled water).
- Pros: Significantly faster and more accurate than manual filling. Reduces the risk of overfilling and underfilling. Less labor-intensive than manual methods. Minimizes the risk of acid spills.
- Cons: Higher initial cost compared to manual fillers. Requires installation, which can take time and may require some technical expertise. The tubing and valves can be prone to leaks, clogs, or damage, requiring periodic inspection and replacement of forklift battery watering system parts. (Image: A single-point watering system installed on a forklift battery. Image text: “Single-Point Watering: Faster and More Accurate, but Requires Installation”)
- Automatic Battery Watering Systems:
- Description: These are the most advanced (and expensive) options. They use sensors to monitor the electrolyte level in each cell and automatically add water as needed. They typically include a water deionizer to ensure water purity. They may even have features like automatic shut-off and alerts for low water levels or system malfunctions. They represent the most sophisticated type of battery-filling system.
- Pros: The most accurate and efficient watering method. Eliminates virtually all manual labor associated with watering. Minimizes the risk of errors and ensures optimal battery performance.
- Cons: The highest initial cost. Requires professional installation and occasional maintenance. (Image: An automatic battery watering system. Image text: “Automatic Watering: The Most Convenient, but Also the Most Expensive”)
- Water Deionizers:
- Description: To use pure water to water the batteries.
- Pros: Protect batteries from damage caused by minerals.
- Cons: Additional cost. (Image: Water Deionizers. Image text: “Use pure water for watering”)
Choosing the Right System: A small operation with only a few forklifts might find a manual battery waterer sufficient despite the labor involved. A larger warehouse with a fleet of dozens of pallet jacks would benefit significantly from a single-point or even an automatic system.
Calculating the True Cost of a Battery Filling System: Beyond the Sticker Price
It’s a common mistake to focus solely on the purchase price of a battery watering kit. The actual cost of lead-acid battery watering extends far beyond that initial investment. You need to factor in all the associated expenses over the lifespan of your forklift fleet. A Total Cost of Ownership (TCO) analysis becomes essential.
Here’s a breakdown of the key cost components:
- Initial Purchase Price: This is the upfront cost of the watering kit or system itself.
- Installation Costs: Labor costs for installing more complex systems.
- Ongoing Labor Costs: Le most significant hidden cost, especially manual watering.
- Water Costs: Distilled water or deionizer operation.
- Replacement Parts: Tubes, valves, floats, etc.
- Downtime Costs: Forklifts are out of service during watering.
- Safety Equipment and Training: PPE and training for handling battery acid.
- Battery Replacements: Improper watering leads to a decrease in battery life.
Simplified Cost Comparison (Annual Estimates):
Facteur de coût | Manual Filling | Single-Point | Automatic | Notes |
Initial (Kit/System) | $50 – $100 | $300 – $800 | $1,000+ | Varies widely. |
Installation | $0 | $100 – $300 | $200+ | Labor costs. |
Labor (Watering) | $500 – $1,000+ | $100 – $300 | $0 – $100 | Manual filling is extremely labor-intensive. |
Water/Deionizer | $50 – $100 | $50 – $100 | $50 – $100 | Consistent cost regardless of system. |
Pièces détachées | $0 – $20 | $20 – $100 | $50 – $200 | Ongoing maintenance. |
Downtime | $200 – $500+ | $50 – $100 | $0 – $50 | Often overlooked, but a significant expense. |
Total Annual | $800 – $1,720+ | $520 – $1,300 | $300 – $900+ | Manual filling is often the most expensive in the long run. |
Discover Advanced Lithium Battery Solutions
Explore SWBATT‘s innovative LifePO4 batteries for electric vehicles, energy storage, and more. Tailored solutions to meet your energy needs with efficiency and sustainability.
Eliminate Watering: The Advantages of Lithium-Ion Forklift Batteries
Eliminating the need for watering is the most effective way to eliminate the costs and complexities of lead-acid battery watering. This is precisely what lithium-ion forklift batteries offer.
Lithium-ion batteries are completely sealed units. They do not require watering, period. This fundamental difference in design and chemistry provides a multitude of benefits:
Zero Watering Costs:
- You can eliminate all expenses associated with battery watering kits, forktruck battery watering systems, forklift battery fillers, distilled water, deionizers, and forklift battery watering system parts.
Zero Watering Labor:
Your employees can focus on their core responsibilities.
Zero Risk of Acid Spills:
- Lithium-ion batteries do not contain liquid acid.
Zero Risk of Over/Underfilling:
The sealed design eliminates human error.
Reduced Downtime:
- No time is wasted on watering.
Simplified Operations:
Streamline battery management.
Lithium-Ion vs. Lead-Acid: Performance and ROI Advantages, a Complete Picture
Eliminating watering is just one advantage. Lithium-ion batteries also offer:
- Durée de vie plus longue : 2-3x+ longer than lead-acid.
- Chargement plus rapide : 1-3 hours vs. 8-10 hours + cool-down.
- Charge d'opportunité : Top-up during breaks – no battery swaps. This is a key differentiator.
- Consistent Power Delivery: No voltage sag, unlike lead acid.
- Poids plus léger : Improved maneuverability and ergonomics.
- Better Cold Performance: More reliable in cold storage environments.
- Built-in Battery Management System (BMS): Enhances safety and optimizes performance.
Your Questions About Battery Watering and Lithium-Ion Answered(FAQs)
Do I need a battery watering kit using lead-acid forklift batteries?
Answer: Yes. Regular, correct watering with distilled water is essential for lead-acid battery health and longevity. A battery waterer is not optional; it’s a requirement to prevent premature failure.
What’s the best type of forklift watering system for my lead-acid batteries?
Answer: The “best” system depends on your budget and operation size. Manual fillers are the cheapest initially but the most labor-intensive. Automatic systems are the most convenient but most expensive upfront. Single-point systems are a good middle ground. However, all watering systems become obsolete with lithium-ion.
Can switching to lithium-ion save me money, even with the higher upfront cost?
Answer: In almost all cases, yes. The total cost of ownership (TCO) is typically much lower for lithium-ion due to longer lifespan, eliminated maintenance (including watering), faster charging, and increased uptime. A detailed, personalized TCO calculation will demonstrate this.
Making the Switch: Is Lithium-Ion Right for Your Fleet?
Consider the long-term cost and efficiency. Conclusion: Embracing the Future of Forklift Power – Water-Free
Battery watering kits et forklift watering systems are necessary expenses only if you’re using outdated lead-acid technology. They represent a recurring cost, a constant maintenance headache, and a potential source of downtime. Lithium-ion batteries offer a fundamentally superior solution: a water-free, maintenance-free, and higher-performance power source for your electric forklift fleet. The future of material handling is efficient, streamlined, and powered by lithium-ion.