Introduction
As a leading manufacturer of lithium-ion batteries for electric forklifts, understand that the industrial battery charger is more than just an accessory. It’s a critical component of your entire material handling operation, directly impacting uptime, battery lifespan, energy efficiency, and bottom line. [In case you are interested in forklift battery voltage, you can browse this article “forklift battery voltage:a comprehensive guide to choosing the right type“]
This guide is for B2B decision-makers – forklift dealers, brand owners, warehouse managers, and logistics professionals – responsible for selecting, purchasing, and managing industrial battery chargers. We’ll cover:
- The different types of industrial battery chargers.
- How industrial battery chargers work.
- Lead-acid vs. lithium-ion charging requirements.
- Key factors in charger selection.
- Long-term cost implications.
We aim for clear, objective, and actionable information. We’ll avoid jargon and focus on practical implications. We specialize in lithium-ion, but we’ll present a balanced view of charging options, acknowledging lead-acid’s role (while highlighting lithium-ion’s advantages).
Understanding the Landscape: Types of Industrial Battery Chargers
“Industrial battery chargers” encompass a wide range of equipment. They can be categorized by:
- Charging Technology:
- Ferroresonant Chargers: Older technology, robust, and relatively inexpensive.
- Pros: Simple, reliable, lower cost.
- Cons: Less efficient (70-85%) [Source: Battery University – Ferroresonant Chargers], more significant, heavier, more heat, less precise.
- SCR (Silicon-Controlled Rectifier) Chargers: SCRs control electricity flow, offering better efficiency and control.
- Pros: More efficient than ferroresonant (85-90%), more precise.
- Cons: More complex, sensitive to power fluctuations.
- High-Frequency (HF) Chargers / Switch-Mode Chargers: Most modern and efficient. Use high-frequency switching for smaller, lighter, and more efficient designs.
- Pros: Highest efficiency (90-95%+) [Source: EnerSys – NexSys Chargers – Example, replace with a relevant source if possible], smaller, lighter, precise control, data logging, communication. Opportunity charge capable.
- Cons: Higher initial cost.
- Ferroresonant Chargers: Older technology, robust, and relatively inexpensive.
- Voltage and Amperage:
- Voltage: Chargers are designed for specific battery voltages (e.g., 12V, 24V, 36V, 48V, 80V). Matching is critical. An industrial 24vdc battery charger is typical for smaller pallet jacks and some forklifts. [Internal Link: Link to a page on your site listing 24V battery options]
- Amperage: Determines charging current. Higher amperage = faster charging, but it needs robust electrical infrastructure.
- Application:
- Industrial Forklift Battery Chargers: These are specifically for forklift batteries, often with features like automatic equalization (lead-acid) and BMS communication (lithium-ion). [Internal Link: Link to your forklift battery charger product page]
- Other Industrial Applications: Chargers for AGVs, scrubbers, sweepers, etc.
- Mounting and Enclosure:
- Portable, wall-mounted, stand-mounted, weatherproof.
- Brand
- For example, industrial battery chargers are too kind.
How Do Industrial Battery Chargers Work? The Basics
All industrial battery chargers convert alternating current (AC) power from the grid to the battery’s direct current (DC) power.
Simplified process:
- AC Input: AC power from an outlet or industrial supply.
- Rectification: AC to DC conversion (diodes, SCRs, or transistors).
- Voltage/Current Regulation: Matches charger output to battery needs. Different technologies (ferroresonance, SCR, HF) do this differently.
- Charging Algorithm: Follows a profile optimized for battery chemistry (lead-acid or lithium-ion) and state of charge.
- Monitoring and Control: Advanced chargers monitor voltage, current, temperature, and state of charge, adjusting as needed. Crucial for lithium-ion (BMS interaction).
- Connection: Safe and correct connection between charger and battery.
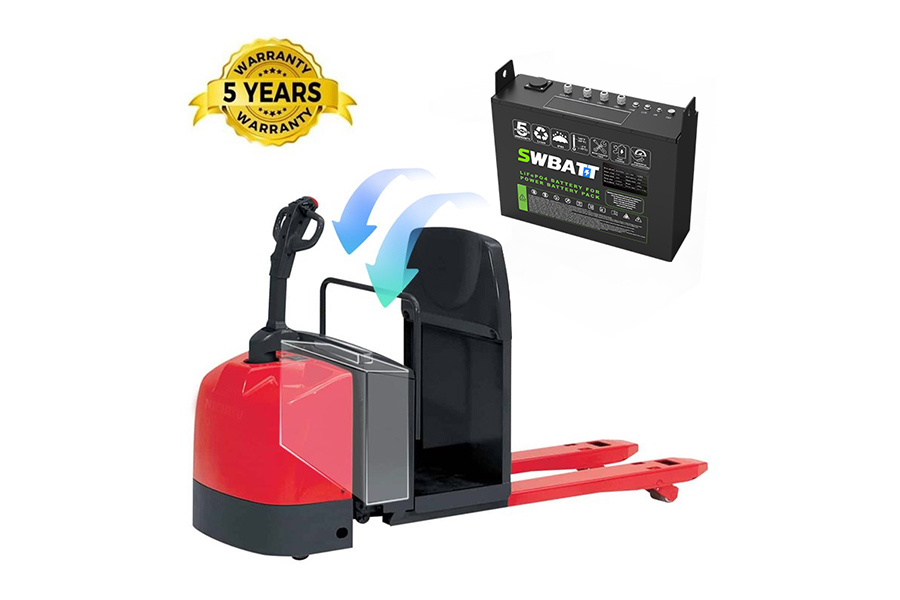
Lead-Acid vs. Lithium-Ion Charging: Key Differences (Table)
Key Takeaway: Lithium-ion charging is more sophisticated, efficient, and safer due to BMS control. Lead-acid is more forgiving in some ways but needs more maintenance.
Feature | Lead-Acid Charging | Lithium-Ion Charging | Source |
Algorithm | Multi-stage (bulk, absorption, float, equalization) | Constant Current/Constant Voltage (CC/CV) controlled by BMS | Battery University – Charging Lead Acid , Battery University – Charging Lithium-ion |
Voltage Control | Less precise | Very precise | |
Overcharge Risk | Higher | Lower (due to BMS) | |
Watering | Required | Not required | OSHA – Battery Charging Safety |
Equalization | Required (periodic overcharging) | Not required (BMS handles) | |
Opportunity Charging | Generally not recommended | Highly recommended | |
Charger Type | Ferroresonant, SCR, or HF (lead-acid specific) | High-Frequency (HF) with BMS communication | |
Efficiency | Typically lower (70%-90%) | Typically higher (90%-98+%) | |
Gassing | Significant hydrogen gas (ventilation needed) | Minimal |
Discover Advanced Lithium Battery Solutions
Explore SWBATT‘s innovative LifePO4 batteries for electric vehicles, energy storage, and more. Tailored solutions to meet your energy needs with efficiency and sustainability.
Choosing the Right Industrial Battery Charger: Factors to Consider
Selecting the correct industrial battery charger:
- Battery Chemistry: Lead-acid or lithium-ion? Crucial.
- Battery Voltage and Capacity: Match voltage (24V, 36V, etc.) and capacity (Ah).
- Charging Time: Faster charging needs higher amperage potentially better infrastructure.
- Shifts/Duty Cycle: One, two, or three shifts? Impacts charging strategy.
- Electrical Infrastructure: Single-phase or three-phase? Amperage capacity?
- Budget: Initial price and long-term operating costs.
- Features: Data logging, remote monitoring, fleet management integration?
- Safety standards and regulations.
- Plug and connector types.
The Long-Term Cost: More Than Just the Charger Price
The industrial battery charger price is only part of the total cost of ownership (TCO):
- Purchase Price: Upfront cost.
- Installation: If applicable.
- Energy Costs: Efficiency matters! Higher efficiency = lower electricity bills.
- Maintenance: Charger repairs.
- Battery Lifespan: A poor charger can shorten battery life, which is a significant expense. A good charger, especially for lithium-ion, can extend it.
- Labor cost.
- Consider heavy-duty industrial battery chargers for long-term run.
Example: Inefficiency’s Hidden Cost
Two chargers:
- Charger A: Cheaper, 75% efficiency.
- Charger B: More expensive, 95% efficiency.
Over a year, Charger B’s higher efficiency could save hundreds, even thousands of dollars in electricity per forklift, quickly offsetting the higher price.
Lithium-Ion and the Future of Industrial Charging
Lithium-ion batteries are driving a shift towards high-frequency industrial forklift battery chargers. These are more efficient and offer the precise control and communication needed for lithium-ion.
Key benefits & charging impacts:
- Opportunity Charging: Top-ups during breaks eliminate battery swaps, changing warehouse logistics.
- Faster Charge Times: Less downtime.
- BMS Integration: Chargers communicate with the BMS for optimal charging and safety.
- Higher Efficiency: Lower energy costs.
- Simplified Operation
Your Frequently Asked Questions (FAQs) About Industrial Battery Chargers
Can I use an old lead-acid charger for a lithium-ion battery?
Answer: No, it’s critical. Lead-acid and lithium-ion batteries have completely different charging needs. Using the wrong charger can severely damage a lithium-ion battery, cause a fire, and void the warranty.
What’s ‘conventional’ vs. ‘opportunity’ charging?
Answer:Conventional: Fully discharge (20-30%), then fully recharge (lead-acid).Opportunity: Top-up during breaks (lithium-ion, needs HF charger).
How do I know the right charger size (voltage and amperage)?
Answer: Match the charger voltage to your battery voltage. Amperage determines speed. Consult manuals or a specialist. Too low amperage = slow charging. Too high (for lead-acid) = damage. For lithium-ion, the BMS regulates, but correct sizing is still essential. We could help you.
Conclusion: Powering the Future – Informed Charger Choices
Your industrial battery charger choice has a significant impact. Understanding charger types, battery chemistry needs, and long-term costs helps you optimize performance, minimize downtime, and improve your bottom line. While lead-acid and its chargers still exist, lithium-ion and high-frequency chargers are the future of efficient, safe, and cost-effective industrial charging. Contact us today for a free consultation and quote on a lithium-ion battery and charger solution tailored to your needs.