Selecting a 48V lithium-ion battery charger for golf carts, whether for your product line or distribution, is more than just a plug-and-play decision. The correct charger directly impacts battery lifespan, performance, and customer satisfaction. This guide provides a deep dive into the technical aspects of 48V lithium golf cart chargers, covering charging principles, design considerations, and key selection criteria – all from an engineer’s perspective. SWBATT is committed to delivering high-quality, dependable charging solutions, and this guide reflects that commitment. We present the information to help you feel more confident and make the right decision.
Understanding Lithium-Ion Battery Charging: The Fundamentals
Table of Contents
ToggleLithium-ion batteries have a different charging profile compared to traditional lead-acid batteries. A multi-stage process is essential for optimal results. Let’s break it down:
- Pre-Charge (Conditional): If a battery is severely discharged (below a specific voltage threshold), the charger initiates a low-current pre-charge. This “wakes up” the battery gently and prepares it for the main charging stages.
- Constant Current (CC) Phase: This is the primary charging phase. The charger delivers a constant, predetermined current to the battery. As the battery charges, its voltage steadily increases. The magnitude of this current (the charge rate) significantly influences both charging speed and overall battery health.
- Constant Voltage (CV) Phase: The charger transitions to continual voltage mode once the battery reaches a predefined voltage (typically around 54.6V for a nominal 48V battery). The voltage is steady, and the current gradually decreases as the battery approaches full capacity.
- Charge Termination: The charger stops the charging process when the current tapers down to a very low level (often a small percentage of the initial CC current). This crucial step prevents overcharging, which can damage the battery.
- Float Charge (Optional): Some chargers offer a float charge stage, maintaining a very low voltage to keep the battery topped off. While this is common for lead-acid batteries, it’s less frequently used with lithium-ion batteries.
A thorough grasp of this CC/CV charging curve is fundamental to choosing and integrating the correct charger.
A 48V lithium golf cart battery charger is a sophisticated piece of power electronics, not merely a simple power supply. It comprises several key components working in concert:
- Input Stage (AC/DC Conversion): This section converts the incoming AC line voltage (typically 110V or 220V) into a DC voltage suitable for charging. High-quality chargers incorporate Power Factor Correction (PFC) to maximize efficiency and minimize harmonic distortion on the power grid.
- Microcontroller (MCU): The MCU is the charger’s “control center.” It orchestrates the charging process, monitors critical battery parameters (voltage, current, temperature), implements safety protocols, and often communicates with the battery’s Battery Management System (BMS).
- Power Stage (DC/DC Conversion): This stage steps down the DC voltage from the input stage to the precise charging voltage and current required by the 48V battery. Efficient designs often employ switching power supply topologies like LLC resonant converters.
- Output Stage: This section delivers the charging current and voltage to the battery. It includes protective circuitry to guard against over-voltage, over-current, and short-circuit conditions.
- Cooling System: Power conversion generates heat. Effective cooling, using either passive heatsinks or active fans (or a combination), is essential for reliable operation and component longevity.
- Communication Interface (Optional): Advanced chargers may feature a communication interface (e.g., CAN bus) to interact with the golf cart’s BMS or other onboard systems. This allows for more sophisticated monitoring and control.
- Battery Management System (BMS) Interaction: An adequately designed charger must seamlessly integrate with the BMS within the lithium battery pack. The BMS provides the charger with crucial data (cell voltages, temperatures, etc.), enabling adaptive and safe charging.
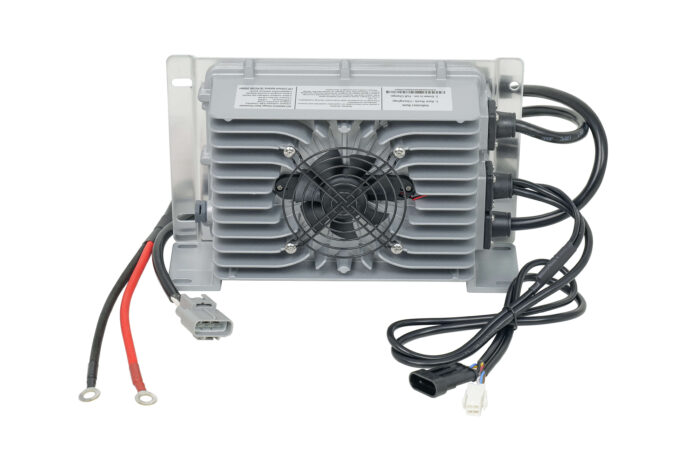
The Impact of Charging Current on Lithium Battery Packs
The charging current, measured in Amps (A), is a critical parameter with a direct influence on both charging time and battery lifespan:
- Charge Time: A higher charging current naturally leads to faster charging. However, high currents can generate excessive heat and potentially accelerate battery degradation.
- Cycle Life: Charging at lower C-rates (a measure of charge/discharge current relative to battery capacity) generally promotes longer cycle life. For instance, a 0.5C charge rate for a 100Ah battery would be 50A, and a 1C rate would be 100A. Always consult the battery manufacturer’s specifications for the recommended charging current range.
- Temperature: Higher charging currents inherently generate more heat. Robust thermal management within the charger and the battery pack is paramount to prevent overheating.
Illustrative Example:
Battery Capacity (Ah) | Charge Current (A) | C-Rate | Approximate Charge Time (Hours) | Impact on Cycle Life | |
100 | 20 | 0.2C | 5 | Excellent | |
100 | 50 | 0.5C | 2 | Good | |
100 | 100 | 1C | 1 | Moderate | |
100 | 150 | 1.5C | Less Than 1 | Not Recommended (Unless specified by the Battery Manufacturer) |
Important Consideration: A well-engineered BMS will protect the battery even if the charger attempts to deliver an excessive current. However, selecting a charger with an appropriate current rating is always the best practice.
Estimating Charge Time and Cycle Life
Charge Time (Approximation): A basic estimate is: Charge Time (hours) = Battery Capacity (Ah) / Charge Current (A). Remember that this is a simplified calculation and doesn’t fully account for the CV phase, where the current gradually decreases.
Cycle Life: Cycle life is typically specified by the battery manufacturer and is influenced by factors such as depth of discharge (DoD), charge/discharge rates, and operating temperature. Deeper discharges and higher charge/discharge rates reduce cycle life.
Best Practices for Charging Lithium Golf Cart Batteries
Avoid Extreme Discharges: Regularly depleting lithium-ion batteries to very low charge levels (e.g., below 20% state of charge) can shorten their operational lifespan.
Partial Charging is Acceptable: Unlike lead-acid batteries, lithium-ion batteries do not require a full charge every time. Partial charging is permissible and, in some cases, may even be beneficial.
Proper Storage: If a golf cart is stored for an extended period, store the battery at a moderate charge (around 40-60%) in a calm, dry environment.
Use the Designated Charger: Always use a charger specifically designed for 48V lithium-ion batteries and ensure it’s compatible with the battery’s BMS. This is not an area to cut corners.
Monitor Temperature: Ensure adequate ventilation around the charger and the battery during charging.
Regular Inspections: Periodically inspect the charger and battery connections for any signs of damage, wear, or corrosion.
Discover Advanced Lithium Battery Solutions
Explore SWBATT‘s innovative LifePO4 batteries for electric vehicles, energy storage, and more. Tailored solutions to meet your energy needs with efficiency and sustainability.
Key Specifications for Selecting a 48V Lithium Golf Cart Battery Charger
When choosing a charger for B2B applications, consider the following critical specifications:
- Input Voltage Range: Ensure compatibility with the local AC power supply (e.g., 100-240VAC).
- Output Voltage: Must precisely match the battery’s nominal voltage (48V) and its charging voltage (typically around 54.6V).
- Output Current: Select an appropriate current rating based on the battery’s capacity and the desired charging time.
- Efficiency: Higher-efficiency chargers minimize energy waste, reduce operating costs, and generate less heat. Look for chargers with PFC.
- Protection Features: Over-voltage, over-current, short-circuit, and over-temperature protection are essential safety features.
- Certifications: Look for relevant safety and regulatory certifications (e.g., UL, CE, FCC) to ensure compliance and quality.
- Communication Interface (Optional): CAN bus or other interfaces can enable advanced monitoring, control, and data logging.
- Warranty and Support: Choose a reputable supplier with a comprehensive warranty and readily available technical support.
- Enclosure and IP Rating: For outdoor or demanding environments, select a charger with an appropriate IP rating (Ingress Protection) to safeguard against dust and moisture.
- Form Factor and Mounting: Consider the physical size and mounting options to ensure proper fit and installation.
- Operating Temperature Range: Verify that the charger can operate reliably within the anticipated temperature range.
Delving Deeper: Charging Algorithms and BMS Synergy
Fine-Tuning the Charging Algorithm
While CC/CV (Constant Current/Constant Voltage) charging forms the foundation, modern 48V lithium battery chargers often employ more sophisticated algorithms to optimize the charging process. These may include:
- Multi-stage CC/CV: Utilizing multiple current levels during the CC phase or multiple voltage levels during the CV phase for further optimization of charging speed and battery health.
- Pulse Charging: Introducing brief rest periods or reverse pulses during charging, which can help mitigate polarization effects and enhance charging efficiency.
- Temperature Compensation: Adjusting the charging voltage and current based on the battery’s temperature to ensure safe and efficient charging under varying environmental conditions. Charging voltage may need to be increased in cold temperatures, while charging current may need to be reduced in hot temperatures.
- Adaptive Charging: The charger dynamically adjusts charging parameters based on the battery’s real-time condition, such as internal resistance, voltage, and temperature.
The Role of the BMS: Beyond Protection
The Battery Management System (BMS) is far more than just a safety device. It plays a crucial role in the 48V lithium battery charging process:
- Battery Monitoring: The BMS continuously monitors the voltage, current, and temperature of each individual cell within the battery pack.
- Balancing: If voltage imbalances exist between cells, the BMS performs a balancing function, ensuring all cells charge and discharge at the same rate.
- Protection: The BMS provides over-voltage, under-voltage, over-current, over-temperature, and short-circuit protection.
- Communication: The BMS communicates with the charger, providing information about the battery’s status and potentially requesting adjustments to charging parameters.
- Data Logging: The BMS can record charge and discharge data, which is valuable for diagnosing issues and optimizing battery performance.
Charger and BMS Collaboration
Effective communication between the 48V lithium battery charger and the BMS is paramount for safe and efficient charging. A common communication protocol is the CAN bus. Via the CAN bus, the charger can receive the following information from the BMS:
- Maximum Allowable Charging Voltage
- Maximum Allowable Charging Current
- Battery Temperature
- Cell Voltages
- State of Charge (SOC)
- State of Health (SOH) The charger can then adapt its charging algorithm based on this data, ensuring the battery remains within its safe operating window.
Thermal Management in Charger Design
Because 48V lithium battery chargers are power electronic devices, effective thermal management is essential. Overheating can reduce efficiency, shorten component lifespans, and even create safety hazards. Common cooling techniques employed in charger designs include:
- Heatsinks: Heatsinks, made from aluminum or other highly conductive materials, draw heat away from power components (e.g., MOSFETs, diodes).
- Fans: Fans force airflow across heatsinks, increasing the rate of heat dissipation. Fan speed can be controlled based on temperature.
- Thermal Interface Materials (TIMs): Thermal pads or thermal paste fill tiny gaps between power components and heatsinks, improving heat transfer efficiency.
- Potting: Encapsulating the entire circuit board or key components in a thermally conductive epoxy resin or other material provides both better heat dissipation and mechanical protection.
- Thermal Protection: Chargers typically incorporate thermal protection circuitry that automatically reduces the charging current or shuts down the charger if temperatures exceed safe thresholds.
Charger Efficiency and Power Factor
For B2B customers, charger efficiency and power factor are important considerations:
- Efficiency: Efficiency represents the percentage of AC input power that the charger successfully converts to DC output power. Higher efficiency translates to less energy wasted, lower operating costs, and reduced heat generation.
- Power Factor (PF): Power factor is a measure of how effectively AC power is being used. An ideal power factor is 1. A low power factor can lead to inefficiencies in the power grid and may result in penalties from utility companies.
Modern 48V lithium battery chargers frequently employ active Power Factor Correction (PFC) circuits to improve power factor and minimize harmonic distortion.
SWBATT 48V Lithium Golf Cart Charger Solutions: Engineered for Performance
SWBATT offers a range of high-performance 48V lithium golf cart battery chargers designed for durability, efficiency, and long-term reliability. Our chargers feature:
- Sophisticated charging algorithms to maximize battery performance and lifespan.
- Robust construction and comprehensive protection features.
- High efficiency and power factor correction (PFC).
- A wide input voltage range for global compatibility.
- Dedicated technical support – we’re here to assist you.
The Next Step: Let’s Discuss Your Charging Needs
Choosing the correct 48V lithium golf cart battery charger is a crucial decision that impacts battery life, performance, and overall cost-effectiveness. This guide has provided a solid technical foundation. Now, let’s talk specifics.
Ready to explore your options? Contact SWBATT today! Our engineers can discuss your 48V lithium battery charging requirements and guide you toward the ideal solution.
[Link to contact page] (Button: Contact SWBATT Engineering)
Interested in a deeper technical dive? Download our white paper on advanced lithium battery charging technologies: [Link to a downloadable PDF white paper]
Would you like to evaluate a sample charger? Request one here: [Link to a sample request form]
We’re committed to helping you achieve optimal charging performance and power your success!
Frequently Asked Questions (FAQs) about 48V Lithium Golf Cart Battery Chargers.
Let’s address some common questions and concerns:
Q1: How long does it take to charge a 48V lithium golf cart battery fully?
A1: It depends on the battery’s capacity (Ah), the charger’s output current (A), and the specific charging algorithm. While a basic calculation is Charge Time (hours) = Battery Capacity (Ah) / Charge Current (A), this doesn’t factor in the Constant Voltage (CV) phase, where the current tapers off. A realistic timeframe with an appropriately sized charger is typically 2-5 hours, but it could be longer or shorter depending on the battery’s initial state of charge and its overall health. Check the battery’s datasheet for the manufacturer’s recommended charge time.
Q2: Is it okay to use a faster charger (higher amperage) to speed up charging?
A2: Potentially, but only if the battery’s BMS (Battery Management System) and the manufacturer’s specifications allow it. Exceeding the maximum recommended charge current can stress the battery, reducing lifespan or damage. The BMS should prevent dangerous overcurrent, but it’s best practice to stay within the recommended limits. Don’t just assume a bigger charger is better!
Q3: My golf cart has 12V accessories. Do I need a separate charger for those?
A3: No, you don’t need a separate charger but a 48V to 12V DC-DC converter (also known as a voltage reducer). This device safely steps down the 48V from the main battery pack to the 12V required by your accessories (lights, radio, etc.). Never connect 12V accessories directly to the 48V battery pack – you’ll likely fry them!